ZEISS - 3D printing precision parts for serial production
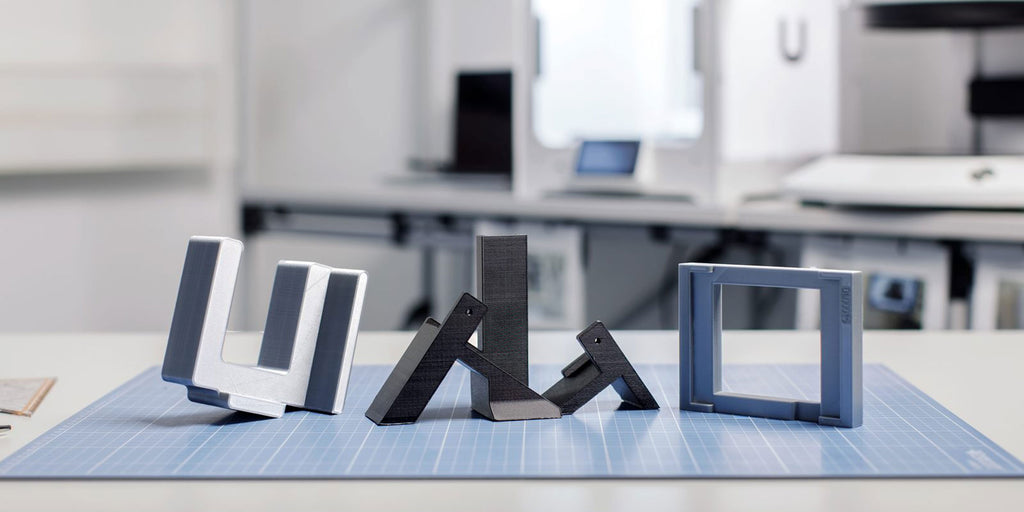
Carl Zeiss Optical Components manufactures microscopes, multi-sensoric machines, and optical sensors for industrial measurement and quality assurance purposes.
Organizations around the world use ZEISS machines to confirm that they produce literally perfect results, every time. That means 'reliability' and 'repeatability' are words to live by at the Wangen, Germany-based company.
Each machine that ZEISS produces is built to align light to optical measurement axes. This alignment is created with brackets and adjustment screws. Each machine, however, requires a different alignment, which meant the ZEISS Team had to complete the work manually.
“This is not a very stable process, and that’s a problem for us. We were looking for a better solution, and found that solution in 3D printing,” Johannes said.
By measuring the angles in a specific machine, the ZEISS team can design and 3D print an adapter plate, which ensures that light travels exactly in the right direction – straight to a device’s sensor – and is critical for obtaining accurate measurements. ZEISS currently 3D prints a unique adapter plate for every microscope in serial production.
Apart from the 3D printed adapter plates, ZEISS have also successfully implemented various other applications within their company, e.g. creating jigs and fixtures for their assembly lines, as well as on-demand printing of spare parts for their clients.
Ultimately, the decision to go with UltiMaker was fairly simple: the machines hit on the company’s two magic words. "The results were reliable, and the results are repeatable," Johannes Grimm, Manager Operational Excellence at Zeiss, said. “That’s important for a stable production process.”
To learn more about how ZEISS successfully integrated UltiMaker 3D printing technology, please click here to visit UltiMaker's application case study.